EXTRAIT DE LA REVUE FORÊTS DE FRANCE
Les produits d’ingénierie en bois augmentent les performances du matériau et valorisent des sciages de qualité intermédiaire. Ces deux avantages expliquent leur succès sur les marchés de la construction.
Qui pouvait imaginer, il y a seulement vingt ans, que l’on construirait à partir du matériau bois des immeubles de grande hauteur ? La tour en bois la plus haute du monde culminera à 84 mètres en Norvège ! Comment est-on parvenu, à partir de la forêt et d’une ressource vieille comme le monde, à un tel niveau de performance ? C’est la conjugaison de progrès techniques qui a permis de sortir le bois de ses usages structurels traditionnels. Le bois massif est forcément limité à la longueur de la grume entrée en scierie : une poutre équarrie ne fera pas plus de 4, 5 ou 6 m. Ces dimensions, qui ont nourri pendant des siècles la charpente traditionnelle, sont désormais largement dépassées. Par aboutage et collage de planches, l’industrie est capable de produire des poutres massives de 14 m de longueur, aussi stables et solides que l’acier. La stabilité dimensionnelle et la résistance mécanique sont essentielles pour construire sur plusieurs niveaux. Or le bois a aujourd’hui réglé ces deux problèmes. Quand il est quasiment impossible de sécher à cœur des pièces de bois massif, il est simple de stabiliser les sciages de 4 cm d’épaisseur qui entrent dans la composition du lamellé-collé. Et le collage de plusieurs épaisseurs améliore la résistance naturelle du bois, à condition de disposer de sciages de qualité.
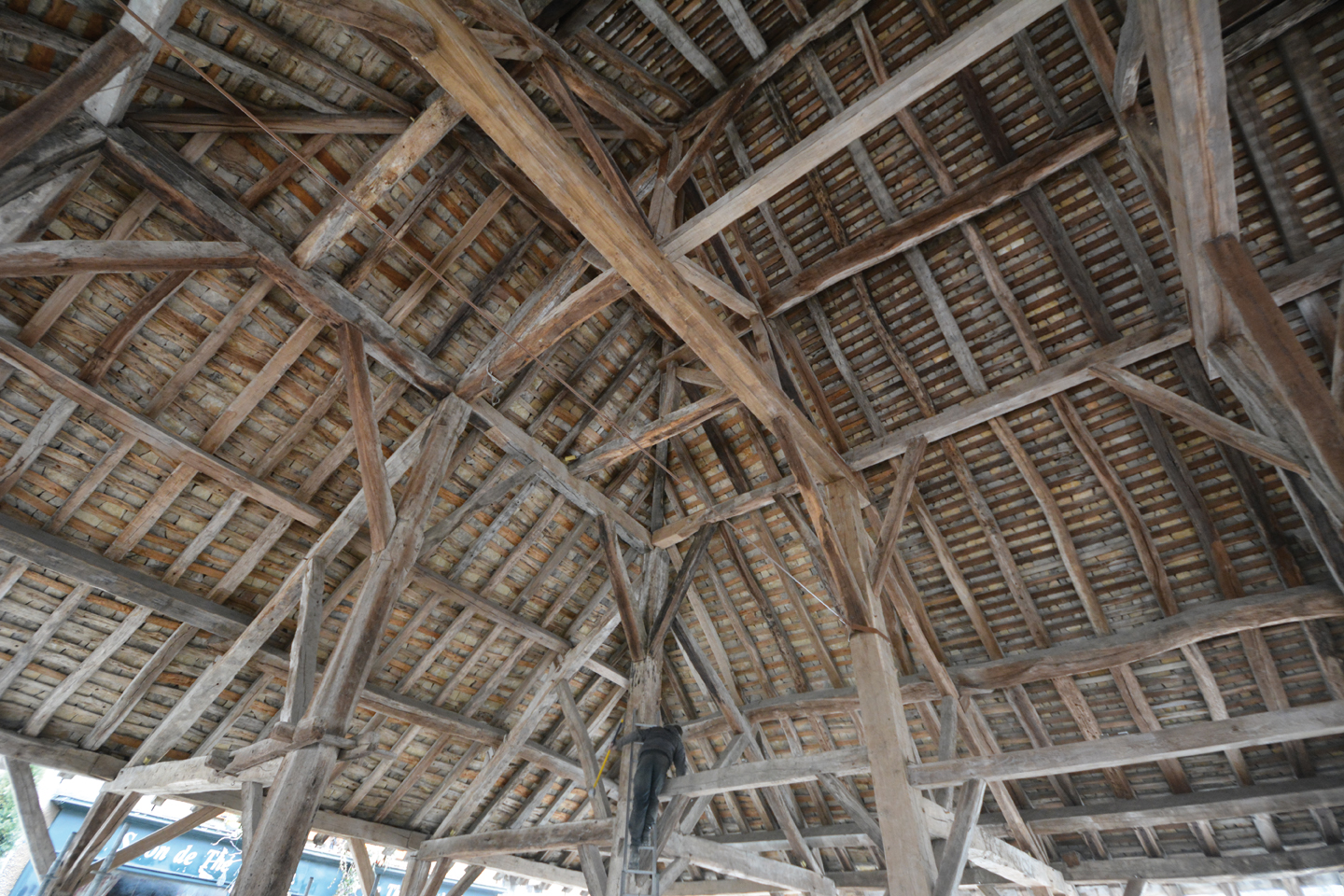
Remplacer l’acier par le bois
Le lamellé-collé a ouvert le champ des possibles au 20e siècle en offrant aux architectes l’opportunité de remplacer l’acier par le bois sur de longues portées. Depuis, les progrès n’ont pas cessé. Les scieurs européens ont investi dans les outils pointus de seconde transformation pour mieux valoriser leurs produits : séchoirs, machines de classement mécanique du bois, chaînes de tri, de collage et de pressage. Les pays scandinaves, l’Allemagne, l’Autriche, valorisent ainsi une ressource résineuse de qualité standard adaptée aux process industriels modernes. La France est entrée dans la compétition plus tard. Plusieurs raisons à cela : dans nos forêts, le feuillu domine, et la ressource résineuse présente des caractéristiques hétérogènes. De plus, peu de scieries possèdent les capacités d’investir dans la seconde transformation. Une bascule s’est opérée en 2008 lorsque Monnet-Sève a construit en Bourgogne une ligne d’aboutage et de collage ultramoderne dans le prolongement de sa scierie résineuse. L’industriel anticipait les besoins de la construction en produits d’ingénierie, mais aussi la montée en puissance du Douglas français : 1 million de mètres cubes de sciages produits en 2017, le double promis en 2035.
L’industrie française du lamellé-collé est performante. Elle produit, bon an, mal an, 200 000 m3 de produits de structure. L’avenir porte moins sur les volumes que sur la matière première qui est encore majoritairement importée d’Europe du Nord. Ses lamelles d’épicéa homogènes, avec peu de nœuds, offrent un rendement meilleur que l’épicéa français. L’enjeu, pour demain, consistera à développer l’usage du Douglas, mais aussi des feuillus, hêtre, chêne et peuplier.
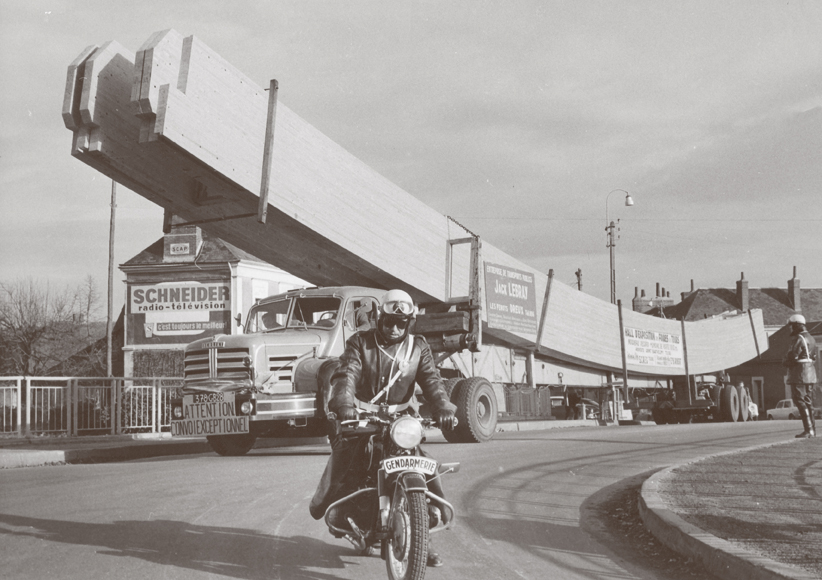
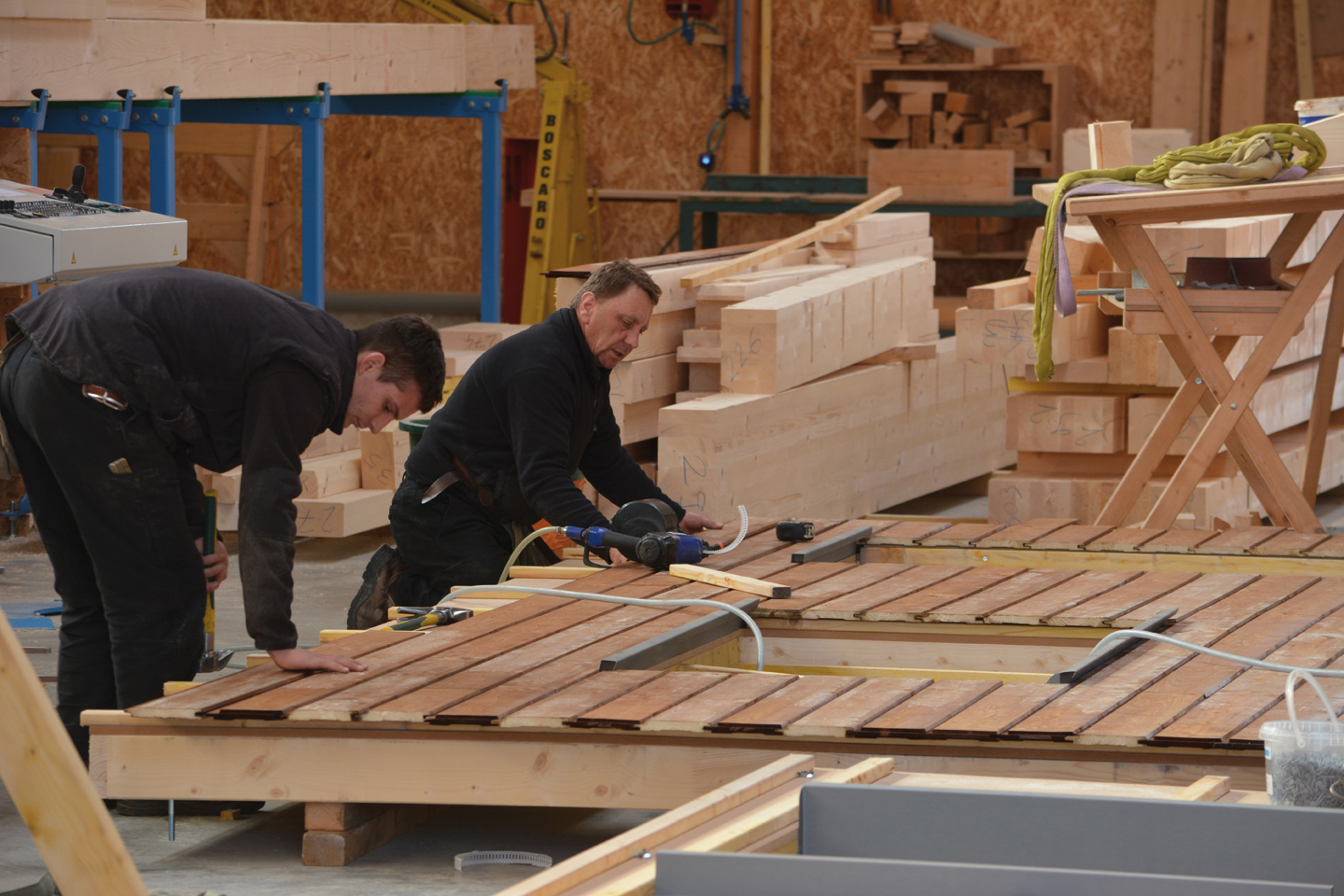
Préfabrication en usine
Les révolutions ne sont pas nombreuses dans le monde du bois. Le lamellé-collé a été inventé au début du 20e siècle, siècle qui s’est achevé avec l’émergence d’un produit tout en un : le panneau contrecollé-croisé.
Dans ce sandwich de sciages, le fait de croiser les couches à 90° augmente la performance du bois. On préfabrique ainsi en usine des murs, des planchers, des toitures. Le CLT, de l’anglais cross laminated timber, permet la construction de modules en trois dimensions – chambres d’hôtel, bureaux, studio étudiant – qu’il suffit d’empiler pour monter un immeuble sur plusieurs niveaux. Après une tentative de développement en maison individuelle, peu concluante sur le plan économique, les constructeurs utilisent le CLT dans ces bâtiments à étages et, depuis peu, pour des constructions plus élevées. Ce positionnement profite de l’émergence des bâtiments durables qui favorisent les bois d’ingénierie biosourcés et bas carbone, et des avancées significatives en termes de conception et de maîtrise des risques incendie et sismique. Le programme des immeubles à vivre en bois prévoit la construction, en France, de treize bâtiments chargés de démontrer les capacités du matériau.
Le plus haut fera quinze étages, et la plupart utilisent des panneaux CLT.
Cette révolution est née chez nos voisins germaniques dans les années 1990.
Depuis près de vingt ans, le CLT est couramment employé en France, mais, là encore, les fabricants nationaux de composants bois ont tardé à se jeter à l’eau. La compétition a véritablement démarré il y a cinq ans entre une petite dizaine de scieurs et constructeurs-fabricants de lamellé-collé. Les premiers ont vu dans le CLT l’opportunité de valoriser des sciages de qualité moyenne, les seconds souhaitent maîtriser la fabrication pour ne plus dépendre des fournisseurs allemands ou autrichiens. Le groupe vendéen Piveteau pourrait récupérer une grande partie du marché national – 40 000 m3 consommés en 2018 – avec une usine entièrement dédiée à la fabrication de CLT. La chaîne entièrement automatisée est capable de produire 50 000 m3 de CLT par an, exclusivement à partir de bois français.Le groupe Piveteau a pris il y a longtemps le virage de la seconde transformation.
« Les produits d’ingénierie sauvent notre métier de scieur, estime son P-DG, Jean Piveteau. Il n’y a quasiment plus de bois massif dans le meuble parce qu’il est compliqué à travailler. Aujourd’hui, les productions industrielles sont automatisées, les process requièrent une matière première stable et calibrée. Les constructeurs utilisateurs de bois massif reconstitué ou de panneaux CLT savent que le produit correspondra parfaitement à leur cahier des charges. Si nous n’étions pas capables de fournir cette matière première “parfaite”, je pense que nous connaîtrions de graves difficultés. »
Pascal Charoy, rédacteur en chef adjoint
du magazine Forêts de France
Cet article provient du dossier Construction bois de la revue de Fransylva,
Forêts de France, n° 622, avril 2019, avec l’aimable autorisation de sa rédaction.
Pour en savoir plus : fransylva.fr
Mensuel Forêts de France
Actualité forestière, opportunités des marchés, évolutions législatives
et fiscales, bonnes pratiques et exemples des autres forestiers.
• Offre découverte : 3 numéros = 10 euros
• Abonnement France 1 an : 10 numéros = 64 euros